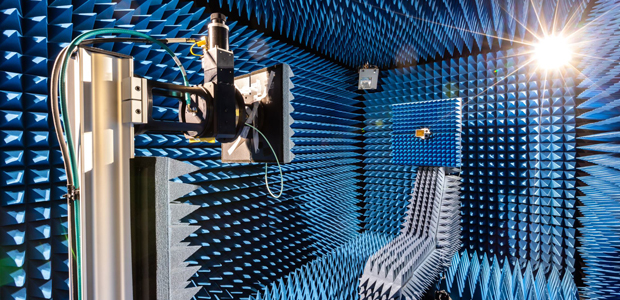
Making the Leap from Prototype to Properly Marketable Product
This is the third in our series tracing the progress of a start-up's first new technology product from detail design through to volume production.
In the previous article, we suggested that having a working prototype puts you about 30% along the road to completion: the point where you can start volume production and shipping units to customers. And, perhaps more importantly, to receiving the revenue that represents the well-deserved return in exchange for your ingenuity and efforts. Now that you have the funding to move forward, what comes next?
There is still work to do, to make the transition from prototype design to production design. To prevent unwelcome surprises in the medium to longer term, it’s particularly important to carefully check the availability and lifetime status of components you have chosen. It may come as a surprise that, even after having created and extensively tested a prototype, it is necessary to evaluate the first batch that comes off the production line equally carefully just in case new problems have arisen in the transfer process. Finally, there is the issue of approvals – both the general CE / UKCA mark required to put the product on the market, and any additional market-specific approvals.
Conversation is Key
Whilst it's easy to go online and check component stocks at any given distributor, this doesn't necessarily give the complete picture. Talking to your preferred supplier can reveal knowledge that doesn’t make it onto the website, such as information manufacturers provide during sales updates or application workshops. Check for any indications of imminent obsolescence, such as an NRND (Not Recommended for New Designs) flag or last-time-buy notice issued to purchasers. Supply shortages and allocation problems are a common occurrence in the industry now and a conversation with a trusted contact is the best way to express your needs and agree on a workable arrangement.
If a component is about to be discontinued, there is usually a reason and often a workaround to meet existing customers’ needs. The response to a problem may be fairly straightforward: if a 64KB microcontroller is no longer available, you may find that the 128KB version is available at a comparable or better price.
It’s also important to talk with your chosen manufacturing partner to finalize the processes that will be used to build the product. You may find that they have more efficient processes than you knew about, for some stages of production, or they may have recently invested in new automation that could accelerate assembly or improve repeatability. Early engagement is recommended, while there may still be time to choose other components or adapt the design to benefit from the new manufacturing processes.
Early engagement with a component supplier is also recommended. You may well have partnered with a supplier and used their design expertise to complete the design, in which case they will be able to offer you the best price. They can also advise on lead times – a difficult issue at the moment. You need a clear understanding of exactly when you need to commit to placing volume orders for the devices you need to support production, otherwise you may well find that you have a production ready design, capacity to build it, but no components to build it with. Buying on the spot market is not recommended.
Building in Bigger Numbers
By now, you may feel ready to begin volume production. We will cover selecting the right manufacturing partner in the next article, but in the meantime let us continue to focus on the product itself. It’s quite common to build a small number of pre-production units as a final check before committing to the full intended volume. Prototypes are built in very low numbers and can be subjected to exceptional attention such as when selecting components and setting up some processes and equipment; particularly those that involve any manual interaction. So, it can be helpful to build a pre-production quantity under conditions that are quite typical of series production to check that the chosen components, tolerances, and manufacturing processes are suited to volume production.
Even after this, it is important to understand that new problems could arise at a later stage of production. Making 100 or 1000 units can reveal additional issues not previously discovered. Even after 10,000 or 20,000 have been built, you may experience new problems. Issues associated with component tolerances are quite common, for example. Components operating at the boundaries of their tolerance can exhibit previously unseen behaviour during normal operation. A supplier may deliver a batch of components that are closer to an upper or lower limit than any before, or alternative or second-source components may differ enough from those delivered previously that a change in operating conditions, like a temperature rise occurring during normal operation, could induce spurious behaviour.
Steve Farmer, of Pharmatechnics, a design consultant with whom Anglia has worked several times, recommends as much testing with prototypes and pre-production units as possible to minimise the risk of issues later. Trialling one unit in the development lab or with a focus group is not sufficient. Testing across all environmental conditions is recommended, as well as at the extremes of the power supply, and with the full range of components that are likely to be used in production. If a new component is introduced, even something simple, test again.
Fly Through Qualification
These pre-production units should be the final form of the product, as it will reach the hands of customers. At this stage, then there is a further step – approvals. Clearly, the units offered for sale must pass all the qualification tests, as these are the ones the market enforcement agencies will take off the shelves to assess. This is also true of other qualifications. For example, if you display the Bluetooth™ logo on your product packaging, you must be able to demonstrate compliance with the standard. Again, the enforcing agencies are known to source products from the market and test them for compliance.
As far as product acceptance testing is concerned, the CE mark or UKCA (UK Conformity Assessed) since the UK left the EU, is a typical minimum requirement to allow products to be put on the UK or European market. Following a period of transition, during which either mark has been deemed acceptable, manufactured products placed on the UK market from 11pm on 31 December 2022 must have UKCA.
For most electronic products, qualifying for the CE mark requires compliance with the EU EMC Directive, 2014/30/EU. The EMC requirements reference tests that are specific to the intended application. The Radio Equipment Directive 2014/53/EU (RED) is relatively new legislation that not only covers electromagnetic compatibility but also ensures safe operation and requires equipment to utilize the radio spectrum efficiently. Industry-specific safety standards must also be met, such as IEC/EN 62368-1 for information-technology and audio-visual equipment. And you must pay attention to applicable eco-design rules, which include restrictions such as the EU ROHS legislation. This typically requires you to gather documentary evidence from suppliers regarding the composition of the components they have provided. On the other hand, mandatory energy consumption and efficiency regulations require you to submit products for testing by an accredited test house.
You must also be aware of market-specific approvals for aerospace, medical, rail, and automotive products. There is the EU’s Medical Device Directive (MDD), while power supplies used in medical equipment that may be connected to a patient or touched by an operator must typically be suitably approved. Note also that your organization will need to demonstrate quality and management systems in accordance with requirements such as the medical industry’s ISO 13485.
The sample you test must be identical to the ones you are planning to produce. Making subsequent changes that may affect the performance in any way is not allowed. It can be inconvenient, therefore, if any serious design changes are needed to pass mandatory testing just as you are ready to go into full production. You should start your product design with full awareness of the standards you need to meet and assess early models and prototypes as rigorously as possible, aiming to leave the test house with zero changes to make.
Conclusion
So, the key steps in taking a product from prototype to volume production are checking the long-term availability of the components required, producing a pre-production batch on the actual production line to be used for volume production, and putting those units through any required qualification or approvals. Now that we understand this, we will move on to consider evaluating and selecting a manufacturing partner in our next article.