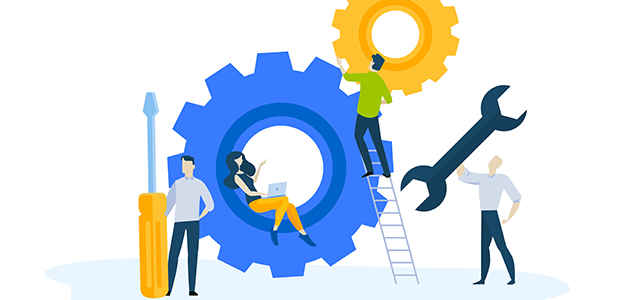
A guide to effective maintenance planning and scheduling
Have you ever heard of making plans and schedules for maintenance? It might sound like a challenging idea, but it's pretty easy.
Picture that you love riding your bike every day. But the chain comes off one day, and the tyres go flat. You can't ride your bike until you fix it. This is why you need to plan and schedule maintenance.
Just like you must fix your bike to keep it in good shape, organisations must take care of their machines and equipment to keep them running well. And this is where the planning and scheduling of maintenance come in. It's like planning how to take care of your bike so it only breaks down sometimes or needs repairs.
In this blog post, we'll discuss how businesses and organisations can use planning and scheduling for maintenance to get the most out of their equipment and keep it running well. So, let's get started!
What is maintenance planning and scheduling?
Maintenance planning
Maintenance planning is an end-to-end process that looks for and solves problems before they happen. This means figuring out what parts and tools are needed for jobs and ensuring they are available and set up correctly. It also means having a planner write instructions for doing a job and figuring out and gathering the necessary parts and tools before a job is given. Planning for maintenance also includes tasks that have to do with features, such as:
- Handling reserve parts
- Ordering non-stock parts
- Staging parts
- Illustrating parts
- Keeping track of breakdowns and lists of vendors
- Quality control (QC) and quality assurance (QA) (QC)
When planning maintenance, you should say ‘what,’ ‘why,’ and ‘how.’ This means saying what work needs to be done and with what materials, tools, and equipment. It also explains why a specific action was chosen (like why a valve was chosen instead of a seat) and how the work should be done.
Maintenance scheduling
Maintenance scheduling is figuring out when work is supposed to be done and who should do it. It has information about ‘when’ and ‘who.’ The goal of scheduling is to:
- Plan the most work possible with the resources you have.
- Schedule jobs based on how important they are.
- Schedule as many preventive maintenance jobs as possible when they are needed.
- Use internal labor well to reduce the contract and outside resources you need.
Importance of maintenance planning and scheduling
Effective maintenance planning and scheduling are important because it helps keep equipment and machines working well for a long time. Just like you need to take care of your toys and games so they last a long time, companies and factories must also care for their equipment and machines. If they don't, the equipment might break down often, which means more repairs and less work getting done.
Steps to effective maintenance planning and scheduling
How do you plan and schedule maintenance in six easy steps? In the rest of this article, we will discuss the implementation process from start to finish. Which can be broken down into the six steps below:
Phase 1: Setup
The setup phase is about ensuring you have everything you need to succeed. You have the support of the leaders, and the right tools are in place. You've made a strong case for change in that you found the key stakeholders and made a first communication plan.
Phase 2: Define
This is where you look at the situation as it is now. You start with the ‘As Is’ and then map out the ‘End State’ you want. ‘To Be,’ as it is called.
Phase 3: Develop
In the third phase, ‘Develop,’ you define your new process, roles, and responsibilities in specifics based on our ‘To Be.’ You make the needed changes to the systems that help (e.g., your CMMS). And you make the programs for training and coaching.
Phase 4: Put the plan into action
This is where things get real. You get the organisation's help. You train and coach your staff until the new way of doing things has become routine.
Phase 5: Close out
Once the change has been made, you evaluate to ensure the planning and scheduling process will last. And improve instead of falling apart when you take a step back. You figure out what you've learned and make a plan to keep the change going.
Phase 6: Sustain
Changing something is easy, but keeping that change is much more complicated. At the end of your application, you must establish the practices that will help you keep what you've implemented going. Think about performance indicators and process reviews done once a year.
Tools for maintenance planning and scheduling
People often consider planning a way to keep things in good shape. Planning doesn't solve all maintenance problems by itself, but it works with other parts and helps keep everything in sync. Let's look at different tools for planning and scheduling maintenance.
Work order systems
A work order system is one of the most valuable tools a maintenance team can use. It acts as a central, automated way for an organisation to ask for and keep track of work that has been done. Work order systems are important because maintenance management must keep track of a lot of work. For instance, a supervisor in charge of eight technicians might do two or three daily tasks for 40 to 60 studies throughout a five-day workweek. Work order systems make it easy for crews and supervisors to talk to each other. A work order system allows supervisors to organise workloads, assign tasks, and track when those tasks are done.
History and data about the equipment
The history and data about the equipment should also be considered tools because they help you figure out what maintenance on equipment is needed based on up-to-date or even real-time data instead of relying on memory or trial and error. Keeping track of industrial maintenance data over time is like having a photo album of the machine's life.
Maintenance metrics
Maintenance metrics are the measurements and scores of activities or results that involve maintenance. They include choosing, gathering, analysing, and showing maintenance data. A standard preventive maintenance metric is the number of work orders in your backlog. Metrics can help with everything from clarifying things to planning for key performance indicators (KPIs), coverage, work type, schedules, compliance, and backlog work hours.
Conclusion
Optimising efficiency through proper maintenance planning and scheduling is important to any organisation seeking to increase output and decrease downtime. By developing a complete strategy that incorporates proactive maintenance, preventive maintenance, and predictive maintenance, organisations can guarantee that their equipment and assets are constantly in good shape. In addition, rational and coordinated scheduling of maintenance activities helps to minimise disruptions to daily operations and maximise uptime. With proper planning and scheduling, organisations can avoid expensive breakdowns and unscheduled downtime, resulting in higher profits and overall success. In today's fast-paced and competitive business world, firms must prioritise maintenance planning and scheduling to fulfill their objectives and maintain a competitive edge.
For more startup news, check out the other articles on the website, and subscribe to the magazine for free. Listen to The Cereal Entrepreneur podcast for more interviews with entrepreneurs and big-hitters in the startup ecosystem.