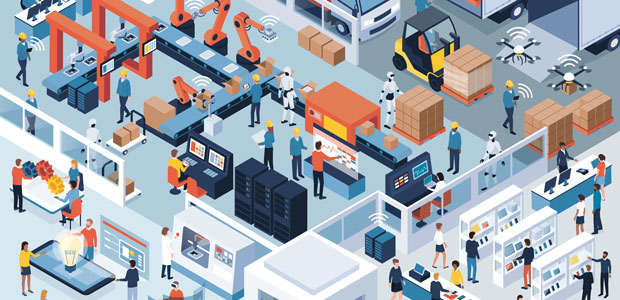
BEUMER Group: Startup Elara supports maintenance
Unplanned machine breakdowns cost time and money. Elara Digital now offers the right solutions for reduced down-times and increased machine availability. Relevant information such as work orders, checklists, machine documentation or guides for trouble shooting can be created in an easy and intuitive way and can be accessed at any time: a knowledge data base for maintenance teams.
BEUMER Group supported the project of the founders and Managing Directors, Akram Alraai and Dominik Adamowski with startup financing.
"Numerous discussions with customers from the manufacturing sector have shown that unplanned machine breakdowns always represent a big problem and can last up to three hours on average," said Akram Alraai who, in collaboration with Dominik Adamowski, founded the Elara Digital in Berlin.
Adamowski mentioned a typical example with a well-known German sports manufacturer: "Because a Profibus component failed, the systems stood still for two hours. The calculated loss amounted to approx. 40,000 Euro."
In order to support the companies in reducing these costs considerably and in increasing the machine availability, the two company founders developed a new solution - a cloud-based software application, which starts with the improvement of the trouble shooting process: getting an overview, orchestrating communication and, in cases of emergency, local access to relevant information.
Elara Digital closes the gap between the maintenance director and the workshop employees. The founders emphasise that their application reduces complexity and provides transparency by equipping the employees in the workshop with a simple mobile application: the factory know-how in your pocket.
A strong partner at your side
The two founders received extensive support also from the Berlin-based, autonomous company builder Beam, a spin-off of BEUMER Group. "We try to solve unique problems in logistics together with the startup teams," explained Managing Director, Robert Bach.
"My task is to find young entrepreneurs with business ideas that are relevant to us. We want to create three startups per year and transform them each into a separate company under the umbrella of Beam - like the Elara Digital GmbH." The aim of BEUMER Group is to open new business areas in logistics together with these companies.
Akram Alraai reported of the beginnings: "BEUMER Group brought us together with more than 30 companies, allowing us to interview them on machine breakdowns and maintenance subjects."
His Co-founder, Dominik Adamowski and he were surprised how painful trouble shooting processes can often be. But what happens exactly? Presuming, the user is operating the BEUMER stretch hood high-capacity packaging system. Suddenly the system stops during the shift. An indicator light starts flashing and the error code xfDE45 appears on the display."
The operator either takes care of the problem or calls a service technician. But no matter who of the two carries out the task, both of them will have to face questions: "Where is the manual for this machine? Where are the checklists and the spare parts lists? Who has carried out the last inspection? What does xfDE45 actually mean? Is there a trouble shooting guide for the current problem?"
Pen and paper slow down digitalisation
It can sometimes take a long time for the employee to have all the information ready. In their discussions with the companies, Akram Alraai and Dominik Adamowski were able to identify some of the main causes of these time wasters: "Often predictive maintenance is missing," said Adamowski.
"This means: The technicians repair defective components and replace the bad ones only if really necessary or at fixed intervals, but not at intervals based on empirical values." This usually requires auxiliary means such as Internet of Things or big-data analysis. The implementation is too complex and time-consuming for many companies. Often, work orders, trouble shooting guides or checklists are handwritten and filled in laboriously.
There is not only the risk of mistakes due to unreadable handwriting, but these documents also have to be scanned in order to be filed digitally. "Companies would like to have a system for easy order processing in maintenance," described Alraai. "Electronic maintenance schedules or checklists should not be put on paper first, but directly into the system."
During the discussions, the two founders also learned how the maintenance topic has changed especially in the COVID-19 pandemic. In order to adhere to the distance rules, many companies switched to shift operation. The result: the personnel cover is thinner in each shift and therefore less employees are available for quick repairs.
Moving towards more efficiency
"We have started here," said Akram Alraai. "Our software allows to create digital work and maintenance orders in easy and fast way and to directly assign them to the right employee."
"He can start working directly with his smartphone: He scans the QR code at the machine or system and can immediately access all relevant data required for example for inspection or trouble shooting. In order to find the required document even faster, he can call it up via voice command," said Adamowski.
"In case of unexpected problems in production, employees often refer to trouble shooting guides and if these are not available, it is possible to upload pictures and videos. This makes it easier to diagnose the problem and then solve it. The software records all possible malfunctions and communicates them," described Adamowski. "Thus the employee has the entire know-how on his smartphone."
The web application permits the maintenance director to have an overview on all machines and employees in operation. On the display, he can also call up all important figures to determine the activities in the workshop. Reports and protocols can be generated and exported in different languages via the app with the help of artificial intelligence. Thus they can be easily transferred to existing systems.
Shared knowledge is more knowledge
Headword Knowledge Sharing Economy: "On our platform we want to make the manufactuer's digital information, such as manuals or tutorials, accessible to our customers," said Adamowski.
"At this regard, we offer an interface through which their documents can be uploaded. Machine operators can also upload and share their reports on faults and how to fix them."
This way, the knowledge database is continuously filled with practically applicable know-how. Data security plays a very important role: the data are anonymised, protected and stored on servers in Germany. Thus, every user can access checklists, manuals or guides and benefit from a large pool of knowledge and expertise.
With the startup, BEUMER Group can successfully pursue its goal of bringing digital solutions into the corporate group. The system provider can now provide its customers with even better support, strengthening its position as partner on the market. The two company founders Akram Alraai and Dominik Adamowski have calculated that users need up to 1.5 hours less for trouble shooting than without virtual assistant.
This can save them up to 30,000 euros on average. And Elara Digital? "We benefit from the cooperation with BEUMER Group in the form of generous startup financing, an extensive network of experts and customers, and a great deal of know-how," Akram Alraai said happily. "We are now part of the BEUMER family."