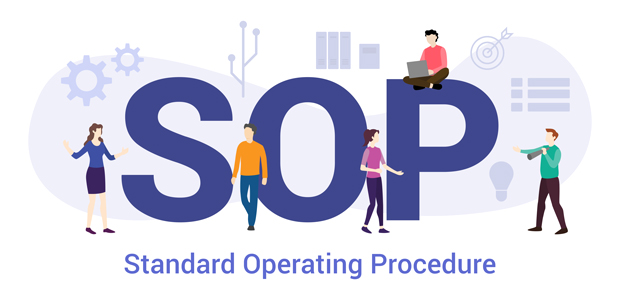
Writing Actionable SOPs: 4 Do's And Don'ts
As your startup grows, standardising work becomes increasingly important.
There’s no better way to ensure consistency in business performance and service delivery than through strong standard operating procedures (SOP) combined with proper employee training.
When implemented correctly, the SOP methodology will save you time, money, energy, and streamline your operations. However, it’s essential to use them correctly to prevent them from backfiring at you.
With that in mind, let’s discuss the do’s and don'ts if you’re planning to implement SOP in your working environment.
Do #1: Go digital
If you plan to introduce a new SOP in a physical form, get ready to deal with a plethora of inefficiencies: overabundant paperwork, clunky physical documents getting lost or damaged, and the constant necessity of overseeing the entire process.
These problems can easily be circumvented with the help of SOP software tools available on the market. As a nice bonus, digital systems are more secure, automated, and supported with various controls to ensure the quality of execution.
Additionally, it’s much easier to implement, with optimal guidelines and premade SOP templates that can be modified to your preferences.
The biggest advantage of keeping digital SOPs is their accessibility. If you want employees to follow specific procedures, they NEED to be easily accessible.
Do #2: Value the feedback
The complexity and timing of the processes vary wildly, which prevents some business processes from being standardized.
The feedback of your employees and team members is effective for improving. Once you implement the SOPs in your work environment, it will not be perfect from the get-go.
To weed out all the inconsistent parts — like bottlenecks or unclear instructions — all you have to do is listen to the people who deal with the system every day.
Understandably, not all feedback might be pertinent. It’s essential to distinguish objective criticism from subjective complaints. But with the proper analysis, you might receive streamlining opportunities that will simplify the entire process with minimum effort.
Do #3: Simplify and visualise
While dealing with the difficulties of implementing and maintaining fluent SOP is crucial, we mustn’t overlook the target audience — the members of your organisation.
The SOP documentation must be easy to comprehend and intuitive. If the step-by-step instruction provided is difficult to follow, it can cause a contra effect — hindering your progress instead of acting as a catalyst.
Building flowcharts or other visual indicators of the workflow has proven to be successful across industries worldwide, especially for processes that involve any decision-making.
Simple processes can be covered by other types of SOPs: like step-by-step SOPs and hierarchical SOPs.
Do #4: Plan ahead
It’s feasible to divide your SOP implementation into manageable stages. There’s no need to spend a small fortune and disrupt your entire scope of operations.
You can set up an SOP for a single department, team, or process and expand the scope to your convenience.
The goals must be clear:
- What department requires SOP?
- What is the target of that specific SOP implementation?
- How much time will it take?
- How will you train your employees?
- How will you track adherence to the SOP?
You should leave no questions unanswered if you wish to get this right from the get-go.
Don’t #1: Don’t let your team disregard the SOPs
It’s pointless to undergo the process of SOP implementation if the members of your start-up refuse to carry out the outlined instructions.
Therefore, you must carefully explain the benefits and purpose of SOP to your team and get them on the same page. After all, an effective SOP can make daily tasks considerably easier, faster, and safer.
In the case of uncertainty, you can set up various controls to ensure that SOP instructions are carried out accurately. These controls include on-site inspections, time studies, and digital supervision.
Don’t #2: Don’t skimp on training
While SOP is not a complicated concept to digest, it might prove difficult to learn the ropes without proper training. Even if you think that this one standard operating procedure is trivial, you should never skip the training. At the very least, all stakeholders (in the process) should be aware there are specific steps to follow, even for simple tasks.
If the new hires are not adequately prepared, their acclimatisation might cause slowdowns in the workflow for an extended period. More so, they might not get comfortable with the system and subsequently decide to disregard the entire procedure.
Be sure to dedicate the proper time and energy to familiarise your personnel with SOPs during the onboarding process and through iterative (re)training.
Don’t #3: Avoid the red tape
The purpose of implementing SOPs is to simplify and streamline a given process. However, many organisations drop the ball by introducing heavy red tape along with the SOP.
Routine paperwork, unnecessary hierarchies, and a general misunderstanding of the methodology cause fundamental difficulties from the inception.
If the SOPs cause more problems and inefficiencies than they solve, then what is the point of setting them up?
Build a system that serves its purpose swiftly and only intervenes when instructions are necessary. The digital SOP tools will also assist you in avoiding red tape since they automatically record most of the workflow.
Remember: SOPs exist to simplify your process, not complicate them further.
Don’t #4: Don’t place your hopes entirely on the SOP
Finally, we should always keep in mind that every process is a set of various independent variables. To achieve optimal workflow, one must pay appropriate attention to every single one of them.
In other words, the usefulness of standardised operating procedures will always depend on the general quality of your organisation:
- Is your personnel motivated?
- Are they performing above or below expectations?
- Are your equipment and machinery in a suitable condition?
- Are the right tools available when employees need them?
If you do not address the overall productivity of your environment, a few well-written SOPs will not solve underlying fundamental problems.
Parting thoughts
Carefully examine the overall condition of your processes: the personnel, resources, equipment, and other variables. It’s wise to consider implementing SOPs after making sure other essential factors of your workflow are at a required level.
When you’re just starting, SOPs are essential to provide clear and consistent guidelines for performing tasks: they will ensure quality and efficiency, and reduce the risk of making mistakes.