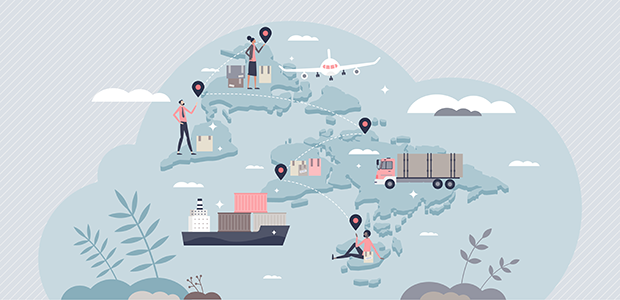
Why PIM is more than just managing product information
The shift from selling products in physical stores to selling products online has made digitalisation and optimisation of product information a must for all participants in supply chains, according to Dr Pat Violaris, Managing Director at OneTimePIM.
Sometimes, product information management (PIM) is neglected by businesses. There are several reasons for this: many organisations consider it a burden on resources, while some see it as an unnecessary necessity that consumes a great deal of time. Others are put off by the perceived complexities of adopting PIM, favouring more established but outdated ways of managing data.
However, PIM can provide much more than just managing product information. When implemented in the right way, they empower employees to transform their efficiency and get things done quicker.
Here are three reasons PIM goes far beyond just managing product information.
Simplification of processes
The primary benefit of implementing a PIM system for many departments is that it simplifies their jobs. The reason for this is that it provides a single point of truth for product information. In practice, this means that workers will always know where to go whenever they need to view or alter data. Furthermore, they know that the PIM contains the most current and accurate information available to their company. This homogenisation of data dramatically reduces the time staff spend on searching for information.
A second important point is that PIM provides much better tools for managing data than most traditional systems. Products are grouped nicely into categories and families, so navigating between items can be done simply and efficiently using filtering. Images for each product are displayed next to the data, providing a visual indicator for the product being edited. Quite simply, it's a much friendlier user interface for all staff who handle data.
Automation of processes
One of the key features of PIM systems is the ability to automate some processes currently done manually by staff. In order to accomplish this, product information is sent directly to websites or sales channels once someone has finished editing it, meaning it is no longer necessary for staff to manually edit multiple CSV files and then upload them into a platform. This is especially useful for more technical products that in the past needed a lot of work to manage.
For example, if you're a manufacturer with retail customers that require regular product information files, these can be sent automatically at a predetermined time. The dreaded data sheets also become a problem of the past, as PIM systems can pull the data needed for the sheet directly and generate it on the go.
Consistent and accurate data
Having no data at all is bad, but having bad data is even worse. A common function of PIM software is to have features in place which enhance the quality of product information. Some of these include:
- Blocking incorrect data from being imported
- Informing users if product data is incomplete
- Keeping units of measurement consistent across the same product type
Essentially, PIM systems work with staff to enable them to identify mistakes, duplications, or inaccuracies in their product data. All of these activities are critical for any organisation serious about its data.
All in all, PIM systems offer so much more than just storing product information. They allow data to flow freely around the company, empowering staff to get tasks done in a timely fashion. Moreover, they ensure the right product data is always in the right place at the right time.
As a result, the time to market for new products is reduced significantly, meaning better productivity and reduced expenditure. This improves staff morale and ultimately enhances the customer experience. This will boost the chances of happy and repeat customers in the long term.