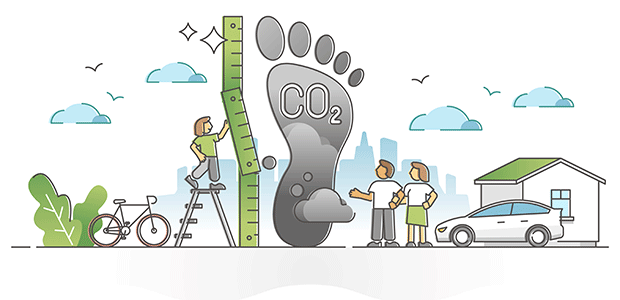
Small business, big carbon footprint?
In 2020, Siemens Smart Infrastructure and WUN H2 partnered up to build a hydrogen production plant in Germany. The plant will run on renewable energy and will be carbon-free, contributing to Germany’s pledge to become gas-neutral by 2050. However exciting the news, Siemens is an established business within automation industry, the road to carbon neutrality is often harder for small manufacturers. Here Neil Ballinger, head of EMEA at automation parts supplier EU Automation, shares some tips.
The Paris Agreement mandates that all signing parties should commit to becoming carbon neutral by 2050. To reach this ambitious goal, many countries have introduced environmental taxes to encourage businesses to operate more sustainably. For example, in the UK, the Climate Change Levy must be paid at its main rate by energy-intensive businesses, while companies investing in energy-efficient technology can apply for tax relief.
Beyond tax reduction, there are other financial benefits to be gained by operating sustainably. Recent research by Make UK shows that before COVID-19, 30% of UK manufacturers were investing in energy saving measures, and that 40% of them reported increased profits as a result.
As good as this sounds, large initial investments and a lack of technical skills can discourage small manufacturers from starting their decarbonisation journeys. However, there are ways to operate more sustainably without breaking the bank.
Energy
Switching to renewable energy sources to power your production lines can dramatically reduce your carbon emissions. For example, the Energy Saving Trust’s solar energy calculator can give you an idea of the return on investment you can expect from installing a solar photovoltaic system.
If you generate your own electricity, you can also apply for payments from your energy supplier through the feed-in-tariff, as well as sell back any extra energy you might generate.
Despite these incentives, small businesses might find that the initial investment is still too high. In this case, a cheaper alternative is to switch to a clean energy supplier.
Though many suppliers offer green tariffs, some are more transparent than others. While a handful of suppliers will sell energy directly from renewable sources, others will simply partake in environmental schemes on your behalf, so it is important to read the small print to understand exactly how green your tariff is.
As well as choosing a clean energy source, you can take steps minimise your energy consumption. An easy and cost-effective way to save energy is to install variable speed drives (VSDs) to AC motors, fans and pumps. VSDs control the speed of rotary equipment to match the effort required for the application, so that the machine does not rotate at 100% capacity unnecessarily.
Waste
Production scrap can be minimised with thorough quality assurance processes. Manual quality assurance carries high error rates and is expensive in the long run. However, innovative machine vision solutions, such as the one proposed by Inspekto, can perform reliable quality assurance with minimal initial investment.
By having several quality assurance stations along the production line, manufacturers can be alerted when a defect occurs, so that the defective item can be removed from the line before further materials and energy are wasted completing it.
For businesses that produce high amounts of organic waste, such as food processing plants, breweries or industrial farms, there are many technologies available to turn your waste into clean energy.
The cost of these technologies can be drastically reduced by investing in community-led projects that benefit a number of small manufacturers. For example, the National Energy Foundation has developed an action plan on how to build a community-based anaerobic digester.
These initiatives alone are not enough to completely decarbonise a small manufacturing plant, but they do demonstrate that with some research and smart planning, small businesses can play an important role in the global fight against climate change.
For more tips on how to reduce the environmental impact of your manufacturing facility, visit EU Automation’s Knowledge Hub.