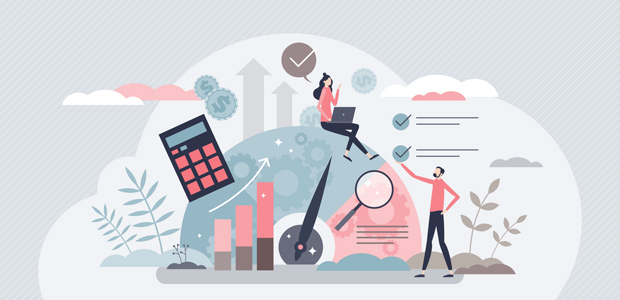
Ten process improvement tools for a more sustainable business
The majority of executives deem sustainability to be important, yet a mere 25% integrate sustainability into the core of their business (according to a BCG/MIT study). The issues stem from the fact that sustainability is considered a business side-branch, and not integrated into the business strategy and model.
Organisations need to write a clear business case for sustainability. To achieve that, businesses should:
- Document their business processes.
- Implement effective process improvement techniques to drive sustainability.
In this article, you’ll learn how to document your business processes, and how to use this documentation to write sustainability into these procedures feeding your organisation.
The top ten process improvement tools given in this article will allow you to make the continuous sustainability improvements needed for true business sustainability.
Documenting your business processes for corporate sustainability
A business process is a collection of linked tasks that find their end in the delivery of a service or product.
Business processes run at the heart of a given organisation. Every business operation performed is done by following a set of linked tasks - aka a business process.
Documenting business processes creates full transparency over your business operations across every department. This transparency can be used to identify areas to make sustainability improvements - and applying the correct process improvement tools will support the effective delivery of the sustainability improvements made.
Before making any improvement though, you need to document your business processes.
Nine simple steps for documenting your business processes
It’s possible to document your business processes using a simple pen-and-paper approach. However, due to the complexity of business operations, your best bet is to use a process documentation software, such as a Business Process Management (BPM) platform.
Once you’ve set yourself up, you can begin documenting your business processes. Follow the below 9 steps:
- Identify and name the process, starting with the core business processes first.
- Define the process scope, i.e. what steps are included in the process and what aren’t?
- Explain the process boundaries, i.e. where does the process begin and end? What causes the process to start? How do you know when the process is done?
- Identify the process inputs, that is, the resources necessary to carry out each process step.
- Brainstorm the process steps by gathering team information from process start to finish.
- Organise the steps sequentially to create a process flow.
- Describe who is involved and responsible for each process task.
- Note down exceptions to the normal process flow.
- Add control points and measurements. This includes identifying process risks or sustainability measures to monitor the process.
Top 10 process improvement tools to create a more sustainable business
Process improvement tools are techniques and methods organisations employ to drive quality improvements. In this article, we’re taking a unique look at these process improvement tools with the question of sustainability in mind.
I’ve split each tool into categories that define the tool type with increasing complexity as follows:
- Process improvement visualisations
- Process improvement exercises
- Process improvement frameworks
- Process improvement methodologies
Note that the process improvement tools given are not to be used in isolation. They supplement each other. Use these tools to create your ultimate process improvement toolbox.
Process improvement visualisations
Let’s start with the basics - process improvement visualisations. Process Improvement visualisations are easy to create and powerful showing how a process can be improved.
Visual information is processed 60,000x faster than text meaning humans remember 40% of what they see as opposed to 20% of what they read. You can use this information to your advantage, to visually represent your business processes and drive sustainability improvements.
Tool #1: Scatter diagram
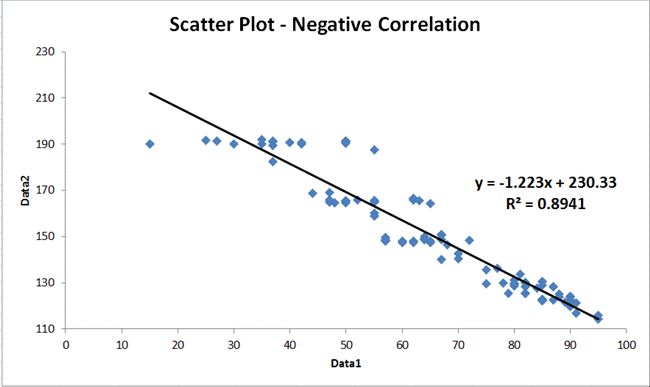
A scatter diagram is a graphical representation showing how one variable changes concerning another. The variables are plotted on right angles to each other, and the degree of point scattering gives a measure of confidence in any correlation shown.
For example, let’s say you introduced a cycle to work scheme. You can then see how this scheme influences workplace Greenhouse Gas (GHG) emission measures (Y variable) over time (X variable). Useful for backing up your sustainability-led alterations.
Tool #2: Checklists
Checklists are a great tool helping you visualise a given business process. Tasks can be viewed in order of completion, with the relationships between different tasks clear.
Coming back to process documentation discussed earlier, you can document any given business process in a checklist format for full transparency over process tasks. This transparency makes it easy for you to apply the required process improvement techniques.
Once more, you can document standards such as those set out by the International Organisation for Standardisation. For instance, the above image represents ISO 14001 standards mapped out in a checklist. This assists internal audit completion, helping organisations check their performance against Environmental, Social, and Economic (ESG) targets.
Process improvement exercises
Process improvement exercises are activities used to assist your sustainability improvement activities.
Process improvement exercises allow you to learn by developing and applying skills, giving context to sustainability targets.
Tool #3: Process baselining
Process baselining provides a starting point, detailing where you're currently operating to make the process improvements necessary.
To carry out process baselining, you need to document your process steps, understand where the process breaks down (breakpoints), and then identify areas of waste.
Process baselining can be used in combination with sustainability benchmarks. Sustainability benchmarks give a reference point to assess trends, measure progress, and baseline global data in a range of sustainability parameters. Benchmarking in sustainability covers a variety of entities, the most common being:
- Sustainability standards, certifications, or similar initiatives or programs, for instance, ISO standards as previously mentioned.
- Priorities, commitments, and performance of companies in the supply chain.
Compare your process baseline to sustainability benchmarks to identify activities that aren’t meeting your objectives.
Tool #4: Gap analysis
Comparing process baselines to sustainability benchmarks will identify gaps in your sustainability performance. You can then use gap analysis as an exercise to clearly define and document this gap.
To complete a gap analysis, you’ll need to define:
- The current situation, or performance.
- Use process baselining to describe your current situation.
- Compare process baselines to sustainability benchmarks.
- Define the reason for the gap analysis.
- Assess current workforce skills and resources.
- The ideal situation, or potential.
- Enter your top organisational goals.
- Identify the relevant skills and resources needed to reach these goals.
- What needs to be done to get from performance to potential, otherwise known as bridging the gap.
- Describe the gap between your current skills and resources and the new ones needed.
- Create an action plan that’ll help you close this gap, and alleviate route causes via root cause analysis (a tool that will be discussed later).
- You can use the PDCA cycle to effectively implement your plan of action, (the PDCA cycle will be discussed later).
Process improvement frameworks
A process improvement framework is a basic structure underlying an improvement concept. By adopting process improvement frameworks, we’re starting to introduce an element of complexity for making the improvements necessary.
However, despite the added complexity, the frameworks given are user-friendly, which is why they’ve made it to my list of top ten tools.
Tool #5: PDCA cycle
PDCA stands for Plan, Do, Check, Act. The cycle details 4 steps for implementing improvements, as follows:
- Plan: The project team determines what they’re planning to change.
- Do: The necessary improvements are made.
- Check: The improved process is compared to the old process to check whether the changes made were improvements at all.
- Act: Everyone involved in the process plays their part in driving the quality improvements necessary.
As mentioned, you can use the PDCA cycle to close the performance gap as identified from running a gap analysis, helping you become more sustainable.
A key aspect to consider when thinking about making sustainability-related improvements is that more can always be done. That is, businesses need to continually assess their current operations and processes to address areas to make sustainability-related improvements. The improvements never stop. Which is where the PDCA cycle comes into its own. As a cycle, the framework is designed to help organisations make continuous process improvements.
Tool #6: Hoshin Kanri
Let’s say you improve the sustainability of your organisation’s processes, how do you ensure these improvements are adopted throughout your organisation?
One means is via utilising the Hoshin Kanri framework, otherwise known as Policy Deployment, which is a strategic planning methodology ensuring everyone in an organisation is driving towards the same goals.
The method will take a given sustainability improvement objective, and break this objective down into smaller objectives, which are broken down further into projects and tasks. These tasks are then distributed throughout your team.
The Hoshin Kanri framework deploys a process called catchball. Despite the jargon term, catchball is a simple idea. Your sustainability purpose, goals, background, and challenges are defined and then thrown between hierarchical levels for opinions, help, and action.
This connects each layer of an organisation and is one of the most effective ways for developing an inclusive culture - e.g. everyone is working towards the same sustainability goal.
Tool #7: Lewin’s Force Field Model
Force field analysis is a change management technique originally conceived by the psychologist Kurt Lewin.
Introducing a new sustainability agenda will impose organisational changes that may not be fully supported by your team.
If you read my last article Why Digital Storytelling is Effective for Promoting Business Sustainability then you'll know that sustainability agendas are likely to face some resistance. Only ⅔’s of US citizens are concerned about climate change. And in the UK, a mere 23% of adults conclude climate change is the most important issue facing the UK in the next 20 years.
Therefore, as part of your process improvement tool kit, you’ll need an effective change management model to assist the sustainability improvement alterations needed. Here I present Lewin’s Force Field Model.
This model provides an overview of a given problem, splitting the problem into factors for and against change. The idea behind the model is that to implement a given change on an organisational level, driving forces need to be boosted and restraining forces alleviated. The model splits the process for implementing changes into 3 stages:
- Stage 1, unfreeze: The changes needed and the business processes affected by these changes are defined.
- Stage 2, make the changes: During the change phase, fresh practices and ideas are exercised. However, the model encourages the user to acknowledge negative emotions that arise during the change period, meeting these emotions with patience and tolerance.
- Stage 3, refreeze the status quo: Once the changes have been deployed, measured, and communicated across the team, and feedback is obtained and acted on, then organisational change is consolidated.
Process improvement methodologies
A methodology is a body of methods, rules, and postulates used in a study area or activity. Once again, we’re increasing the complexity of the tools in our process improvement tools box.
The three methodologies presented below offer a user-friendly and thorough means of improving the sustainability performance of your organisation’s processes.
Tool #8: Root cause analysis
Coming back to the gap analysis discussed earlier, to create a plan of action that closes a given performance gap, you’ll need to get to the root cause, eg. what is causing this gap in the first place?
Using root cause analysis alongside gap analysis will help you meet your sustainability objectives. A common method to implement root cause analysis is via the Fishbone Diagram (Ishikawa diagram) - as presented below.
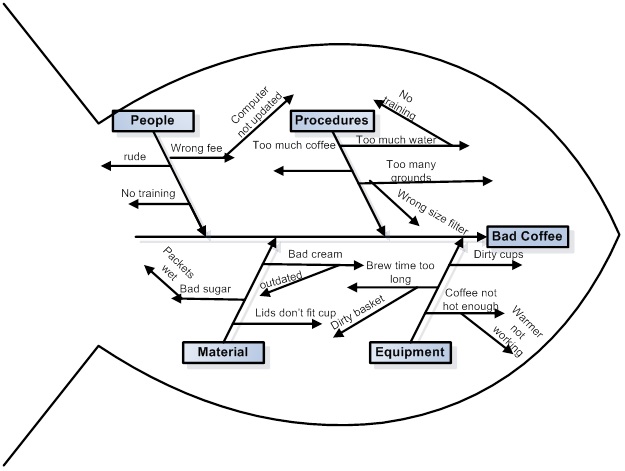
Complete the fishbone diagram using the following steps:
- Identify the problem.
- Brainstorm causal factors.
- Record your main problem at the center of the fishbone diagram (the fish spine). E.g. reduce workplace energy consumption.
- Write down the various potential factors that could cause this problem, arranging these around the central issue as branches (fish rib bones). E.g. poor insulation, not using LEED light bulbs, poor heating controls.
- As you continue to move down the fish spine, you’ll move onto smaller branches and more specific categories, until you eventually reach your root cause.
Tool #9: Heijunka
Heijunka is a Japanese term meaning leveling. Heikjunka helps organisations match unpredictable customer demand patterns to eliminate process waste.
Waste is estimated to costs the UK industry at least £15bn annually. According to most recent government figures, commercial and industrial waste in 2018 was around 37.2 million tonnes, a rise from 36.1 million tonnes in 2017.
Process waste can range from wasted environmental resources sent to landfills, wasted energy use, and wasted time - these hold significant environmental and social costs.
Applying the Heijunka methodology means you’ll take an average output to keep process production consistent. On days where your output is more than needed, you’ll move excess into a fluctuation stock, and pull out from this stock when output falls short of demand.
The Heijunka method improves stock control processes and relies on a carefully calculated production rates.
Tool #10: Lean Six Sigma (DMAIC)
To conclude this article, I’ll finish up with my favorite process improvement tool - Lean Six Sigma.
Lean Six Sigma gives a structural approach to scrutinise business operations, looking at data and processes to uncover and remove waste.
Lean Six Sigma is a process improvement tool that can be applied using DMAIC, which stands for Define, Measure, Analyse, Improve and Control, as explained:
- Define what business operations need to be improved. Eg. What operations produce the most waste? Where can you save energy?
- Measure current process performance. Just like you’ve done during gap analysis.
- Analyse data to determine how the business operation needs to be improved.
- Improve your process continuously. You can implement the PDCA cycle to make continuous improvements.
- Control your processes for ongoing sustainability and optimised performance. Create a system or process to monitor results.
Again, the DMAIC methodology adopts the idea of making continuous process improvements, to improve business sustainability.
Using these top ten process improvement tools will help you consistently improve the sustainability of your business.
Writing sustainability into your business processes will integrate environmentally, socially, and economically responsible practices into the core of your organisation. This will create the business restructuring we need to ensure human stability for our children’s future.