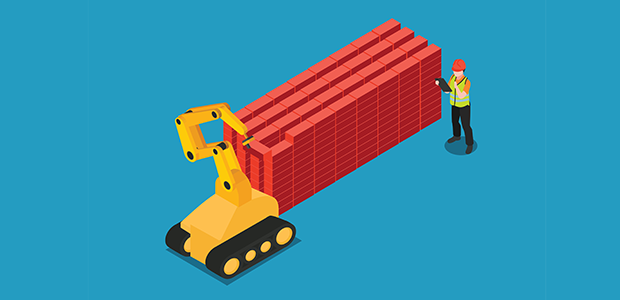
Pop-up robotic micro-factory completes first building
Automated Architecture (AUAR), a construction tech startup, has completed its first project using a pop-up robotic micro-factory, marking a major advancement in the company's mission to make sustainable housing scalable and accessible.
This milestone project, a two-story building for construction group Vandenbussche NV in Belgium, was entirely robotically manufactured and designed using AUAR’s proprietary software and technology, showcasing a future of flexible, high-quality, and sustainable housing.
In partnership with construction group Vandenbussche NV, AUAR completed its first building fully manufactured by a pop-up robotic microfactory. The two-story structure is designed as a housing unit but will be used as an office for Vandenbussche. AUAR’s micro-factory manufactured all structural elements, including walls, floors, and roof, as well as internal division walls. The project was conceived in AUAR’s Master Builder software, which generated both the design and the code that guided the robotic system throughout production. This represents one of the first projects globally to be fully robotically manufactured, and the first globally to be manufactured in a pop-up micro-factory.
“This is the first time that a pop-up robotic micro-factory has built an entire project, including walls, floors, roofs, lintels and interior divisions,” says Gilles Retsin, CTO and Chief Architect at AUAR. “Until now, home builders would have to invest in large facilities and expensive manufacturing lines, but with AUAR’s micro-factories they can do the whole process with a single, compact robotic work-cell, a factory in a box.”
With AUAR’s new V2 Robotic Micro-Factories, the structure can be pre-manufactured in under eight hours, a time that could be reduced to less than three hours when three Micro-Factories work in parallel. The project integrated glulam columns and beams, which served as a test to demonstrate how the system could scale to multi-family housing up to six storeys. The project explored adaptable design elements like varied window sizes and placement to test the flexibility of AUAR’s system. AUAR’s MasterBuilder software allows each building to be uniquely designed, without adding extra cost or losing efficiency in production.
“Today, the need for affordable, sustainable multifamily housing is critical,” said Mollie Claypool, CEO of AUAR. “Our Micro-Factories allow developers and contractors to produce this type of housing at lower costs and reduced time on site, while our software allows us to make each project unique and adapted to the needs of the local community.”
Transforming construction
AUAR’s pop-up micro-factories are a breakthrough in construction automation, using smart but cheap robotics to respond dynamically to design variations and complex building needs. Unlike traditional modular construction, which often requires costly, large-scale facilities, AUAR’s micro-factories are easily deployable, and adaptable for different projects.
“With AUAR’s systems we can automate the construction process for housing, without having to invest heavily in larger facilities and equipment. We robotically manufacture the core and shell of the building, and finish the building on-site, just as we would normally do with brick and concrete,” says Kristof Defruyt, CEO of Vandebussche NV. “This technology empowers us to deliver sustainable timber housing quickly, affordably, and with reduced time on site, meeting the growing demand for cost-effective housing without sacrificing quality.”
AUAR’s Micro-Factories and Master Builder software open new possibilities for developers and contractors in both Europe and North America. The decentralised, adaptable model is a powerful response to global challenges in housing affordability, labour shortages, and CO2 emissions. With AUAR’s technology, housing production can shift from large centralised factories to smaller, distributed production hubs, closer to the communities they serve, minimising transport emissions, supporting local economies, and meeting diverse housing needs.