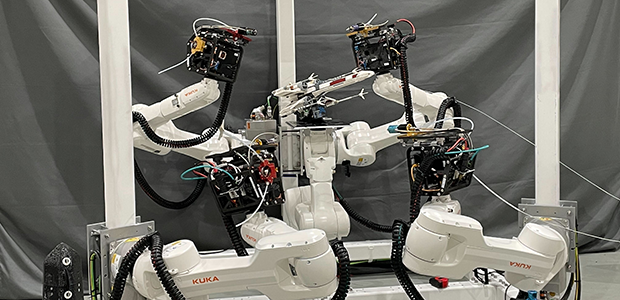
Orbital Composites: redefining the boundaries of manufacturing
Orbital Composites stands at the forefront of technological innovation in the realm of additive manufacturing, a field that's rapidly transforming the landscape of industrial production. Specialising in 3D printing technologies, this startup is pioneering the development of composite materials for space and aerospace applications.
The founder, Cole Nielsen, has a vision for a more sustainable future. He emphasises the need for efficient recycling and the use of a more limited range of materials to reduce waste and environmental impact. He advocates for a radical shift in manufacturing and materials science, suggesting that a focus on carbon fibre, titanium, and high-performance thermoplastics could lead to more sustainable technological development.
“If you go to Mars, you’re not going to take Styrofoam cups,” notes Nielsen.
Orbital Composites is leveraging robotics and additive manufacturing to fabricate components that are essential for satellites, spacecraft, and potentially even space habitats. Its approach promises to significantly reduce the cost, complexity, and logistical hurdles associated with space missions. In space, traditional manufacturing techniques are impractical and expensive, making the lightweight and robust solutions provided by 3D printing particularly valuable.
Nielsen has a vision for future space exploration where we utilise materials from asteroids for future construction. He proposes innovative ideas like converting asteroids into mirrors for spacecraft propulsion.
Humble beginnings
Orbital Composites was founded in 2014. Nielsen studied Satellite Physics and Computational Math at Embry-Riddle Aeronautical University and, from an early age, was influenced by Jerry Lawson, an engineer known for inventing the cartridge-based video game system and being a pioneer in semiconductors and radar technology. This mentorship led Nielsen to Stanford University at the age of 14.
Nielsen started designing 3D printers for large aerospace structures like drones and satellites in his garage. His solution? Robots.
Robotic automation presents a host of significant benefits at a much lower cost compared to conventional manufacturing systems. These advantages include the ability to scale operations and the capability to perform intricate 3D printing on curved surfaces.
Recognising the need to prepare its customers for the advancements of Industry 4.0, it understood the importance of upgrading its technology to synchronise data in real-time across a vast network of Cloud-connected robots and IoT devices.
With these future industry needs in mind, the company introduced Orbital S in 2019, the first robotic 3D printer built for industrial scale. Orbital S is an industrial-grade robotic 3D printer, that enables mass production of large end-use parts. It is built to scale rapidly, so you can build a large robot print factory in no time.
There’s even a smaller, more affordable version for education and research customers. The aim is to make robotic additive manufacturing accessible to all and help train the next-generation workforce. The Orbital e- offers a range of standard features including a six-axis robotic arm, a large 1.2 x 1.2m build platform, and the ability to print with aerospace-grade thermoplastic filaments. The system is equipped with Orb OS, a novel real-time robot control software, enhancing the precision and accuracy of the printing process.
One giant leap for mankind
Back in July 2023, Orbital Composites received a contract valued at $1.7 million from the US Space Force (USSF). This contract was awarded through SpaceWERX and its Orbital Prime initiative, which focuses on accelerating the development of in-space servicing, assembly, and manufacturing (ISAM) technologies.
The company secured a Direct-to-Phase-II Small Business Innovation Research (SBIR) grant, working in partnership with prominent US industry leaders such as Axiom Space in Houston, Texas, Northrop Grumman in Denver, Colorado, and Southwest Research Institute (SwRI) in San Antonio, Texas. As part of this programme, Orbital Composites aims to transform two key areas: Satellite-Based Cellular Broadband (SBCB) and Space-Based Solar Power (SBSP). Its goal is to offer global access to broadband Internet and provide clean energy solutions worldwide.
Amolak Badesha, Co-Founder and CEO, Orbital Composites explained that SBCB requires large antennas, while SBSP necessitates antennas on an even larger scale, extending to kilometres. Both these applications demand manufacturing processes that are not only high in volume but also low in cost, alongside in-space servicing, assembly, and manufacturing (ISAM) capabilities.
Orbital Composites is addressing these requirements by adopting a strategy to manufacture and assemble such antennas directly in space. This method has the potential to significantly lower deployment costs and open up new, groundbreaking commercial prospects. In 2023, Orbital Composites took a decisive step forward by signing a memorandum of understanding (MOU) with Virtus Solis, based in Troy, Michigan, US, to construct the first megawatt-scale station for Space-Based Solar Power.
Receiving the Direct-to-Phase-II SBIR grant from the USSF, Orbital Composites is set to fast-track the advancement of its manufacturing technologies. The company is gearing up to deploy its space factory module within an anticipated timeframe of 3-5 years.
Onwards and upwards
The company is currently looking to expand its team. “I’m trying to build a company that’s based on the principles of operating as a very good family,” states Nielsen. “Finding people to be at the edge of human performance and design is a great challenge.”
For an industry that is historically very conservative, it’s a major mindset change whenever anything new, or revolutionary comes along. “The onus is on you to really show that it’s going to work. This is why we’ve been working on this for a number of years and it’s something you can’t force your way through,” said Badesha.
The focus for Orbital Composites now is to scaleup its manufacturing-as-a-service business, particularly for the aerospace and defence and energy industries. It also has a major target to demonstrate its CMC (Ceramic Matrix Composites) technology for high temperatures through a hypersonic flight test.
This article originally appeared in the January/February issue of Startups Magazine. Click here to subscribe