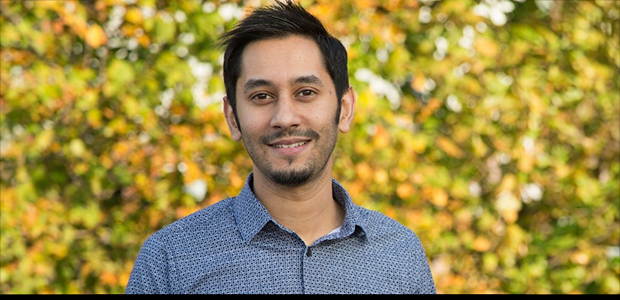
Navigating the transition: how startups can embrace 3D printed plastic prototypes and beyond
In the ever-evolving landscape of startup manufacturing, transitioning from concept to production requires astute decision-making and adaptability. 3D printing has proven invaluable for prototyping plastic parts, offering rapid iteration, design flexibility, and a tooling-free process.
This article originally appeared in the January/February issue of Startups Magazine. Click here to subscribe
Author: Saleem Shariff, Application Engineering Manager – EMEA, Protolabs
However, as startups progress beyond the prototyping phase, many considerations come into play, from selecting the most suitable production technology for your needs to finding the right time to make the leap to manufacturing. Before making any decision, startup manufacturers must unravel the common myths around production methods that can heavily influence their decision-making process.
Dispelling myths and embracing technological evolution
Myth 1: ‘3D printing is only suitable for producing a few parts’
Contrary to popular belief, advancements in automation and production speeds have elevated 3D printing's capabilities, making it a viable solution for producing up to a few hundred parts efficiently and cost-effectively.
Myth 2: ‘3D printing is mainly used for prototyping’
While 3D printing has long been associated with prototyping, its role has expanded into final part production. The advantages it offers during development, such as the cost-effective production of diverse designs, make it increasingly relevant for end-use parts.
Myth 3: ‘Injection moulding tools are expensive’
The myth of excessive injection moulding tooling costs is shattered by using aluminium instead of steel tooling, making injection moulding a cost-effective option for both prototyping and low to mid-volume manufacturing.
Myth 4: ‘It takes a long time to produce injection moulding tools’
Traditional timelines for tooling production are debunked by streamlined, rapid processes, where injection moulding tools can be produced in as little as one to 15 days.
Myth 5: Injection moulding is only suitable for mass production’
The cost advantage of producing aluminium tools challenges the notion that injection moulding is exclusively for mass production. It becomes a viable option for producing hundreds of parts, allowing for thorough design testing before committing to large-scale manufacturing.
Myth 6: Steel tools will last longer than aluminium tools because it is harder wearing
The choice of alloys plays a crucial role, and aerospace-grade aluminium (2024 T351) proves to be harder wearing than some steels. A detailed understanding of tool alloys is imperative for informed decision-making.
Which process is right for you?
The answer depends on where you are in your process and what you are trying to accomplish. As the design progresses, a prototype with the size, finish, colour, shape, strength, durability, and material characteristics of the intended final product becomes increasingly important. Therefore, using the proper prototyping process is critical. To truly understand what option is suitable for your project, you must consider these three things:
- What level of prototype do you require?
- What factor(s) is/are most important to you?
- Will the attributes meet your expectations?
If you know what stage you are at in the prototyping process, you’ve given yourself an excellent foundation for success. If you are in an early stage of concept modelling, then the speed of production and appearance may be your most important factors. Therefore, you want to opt for a process that can meet your quantity and complexity, material choice, surface finish and colour.
Once you progress to an assembly and functional testing stage, the form, fit, chemical resistance, mechanical, electrical, thermal, and optical properties will be the critical factors on your agenda. As a result, you will select your process based on the material choice, stability, tolerance, speed, and quantity.
As the product takes shape and you begin the life and regulatory testing stage, additional factors such as ageing properties (UV, Creep), flammability, food rating, and bio-compatibility come to the fore. Speed, quantity, material choice, stability, and tolerance are at this point.
Factors shaping manufacturing decisions
As startups navigate the complex landscape of manufacturing decisions, several key factors come into play.
Cost: balancing the cost equation involves considering design intricacies, production time, and tooling costs. There are also upfront costs to consider. Injection moulding tooling can be a significant investment, both in terms of time and cost. Streamlined processes that minimise these costs and time are available, providing an excellent option for startups seeking faster, cost-effective solutions.
Design considerations: collaborating with engineers who understand the final manufacturing process becomes crucial during prototyping. Simple geometries may favour injection moulding, while 3D printing excels in creating complex designs.
Material availability: the range of materials available in injection moulding surpasses that of 3D printing. For instance, at Protolabs, we offer hundreds of resin options for injection moulding compared to 14 options as standard for 3D printing.
Different production options for plastic parts
Product development is an iterative process, and as technological advancements continue, the line between prototyping and production becomes fluid. Understanding the nuances of each production option is crucial for startups.
3D printing: beyond its role in prototyping, 3D printing offers a seamless transition to production for lower volumes. The technology's advantages, including design complexity, rapid customisation, and automation advancements, position it as an ideal choice for producing up to a few hundred parts.
Injection moulding: as production volumes increase, injection moulding emerges as a cost-effective solution on a per-part basis. Accelerated injection moulding, with tools produced in just one to 15 days, becomes a compelling option for startups requiring anything from a few hundred to 150,000 parts.
The journey from ideation to production necessitates a reliable and informed partner. Selecting a supplier proficient in 3D printing, injection moulding, and CNC prototyping ensures startups receive unbiased advice and comprehensive support throughout the product development journey.
Moving incrementally towards mass production
Even for startups contemplating traditional injection moulding with steel tooling, an intermediate step with accelerated injection moulding can prove beneficial. Rapid injection moulding provides a strategic option for startups, allowing for rapid design adjustments and faster, cost-effective tooling.
The key is to work with a supplier with the bandwidth to support you throughout your journey, offering a holistic approach to product development where they can support you from the initial design analysis to the final manufacture of parts.
In reality, the journey from 3D-printed plastic prototypes to mass production is nuanced and multifaceted. Startups who think strategically, source unbiased advice, and adopt a flexible mindset can navigate the complexities of product development and manufacturing, ensuring a successful and efficient transition