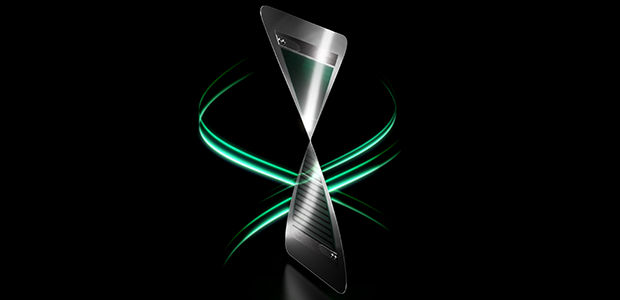
Beating back batteries: Dracula Technologies' energy harvesting tech
The issue of battery waste is pervasive: according to figures shared by Statista, between 2011 – 2021 246,000 metric tonnes of portable batteries and accumulators were sold in the EU, of which 48% were collected for recycling.
Although the same figures cite an increase in battery recycling of 13% since 2021, a quick calculation shows 127,920 weren’t recycled. TheseThe issue of battery waste is pervasive: according to figures shared by Statista, between 2011 – 2021 246,000 metric tonnes of portable batteries and accumulators were sold in the EU, of which 48% were collected for recycling. Although the same figures cite an increase in battery recycling of 13% since 2021, a quick calculation shows 127,920 weren’t recycled. These are figures recorded just within the EU, and not the rest of the world.
Why am I waffling on about batteries and their recycling rates? Simply put, batteries are commonly disposed of, not biodegradable, and often end up in landfill. That’s without taking into account battery production, where the precious materials that make them up are mined from the earth.
Unfortunately, the number of devices that rely on batteries for power – common household items like remote controls and alarm clocks, but also IoT devices like meters and sensors – are everywhere, and global demand for Lithium-ion batteries in particular is projected to increase sevenfold between 2022 – 2030.
Enter Dracula Technologies. The startup, which was founded in 2012 and lends its name from the infamous vampire who thrives in the darkness – much like their energy-harvesting technology, which works in low-light conditions – leverages its tech as an alternative to batteries.
“Dracula Technologies began as a collaborative R&D project between a laboratory and two companies,” Brice Cruchon, CEO, told me. “The objective was to develop a system for printing materials on third-generation photovoltaic cells – cells that don’t rely on silicon or rare earths, making them resource-efficient.”
Like any great project that leads to something with the potential to revolutionise, this led to the creation of their energy-harvesting technology. Energy-harvesting is becoming somewhat of a buzzword in the IoT space as an alternative to batteries that power devices by ‘harvesting’ from energy sources, which could be anything from light to heat to vibrations.
Each energy-harvesting device tends to be nuanced in its approach of how it chooses to harvest energy and, importantly, how it is integrated into a device like a remote control, to replace the conventional battery.
Dracula Technologies’ technology is its LAYER modules, organic photovoltaic (OPV) modules that harvest energy from light, and can operate in low light conditions. A remote control, for example, left out on a coffee table, won’t always be beamed with sunlight and consequently needs to be able to work after shadier days. The modules are also fully recyclable.
“They’re [LAYER modules] ideal for connected objects that require very low power,” Cruchon said. “Our OPV sensors are small, just a few square centimetres, and operate with low brightness, as low as five lux.”
Its LAYER Vault solution, which was launched in early 2024, has two layers, in what the company calls its “two-in-one solution”: the OPV layer harvests ambient light, and the energy storage layer stores harvested energy for later, for these dark periods.
Another aspect of note is how the modules themselves are manufactured. Dracula Technologies uses inkjet printing, which Cruchon cited as providing them with the capability to create customisable designs for customers with high electrical performance. In short, the modules are manufactured with an eye on reducing costs and resources.
“We use organic materials which are environmentally friendly, consuming less than one gram per square metre and emitting just 3kg CO2 equivalent per square metre,” Cruchon noted.
From smart home to asset tracking
From a startup that was founded in 2012 to now – having begun production of its OPV modules at industrial scale this year – the challenges weren’t just in the technical details, like crucially ensuring the modules work, but in getting the funding in the first place, Cruchon told me. I hear a collective sigh from tech startups everywhere
“We achieved funding through technical partnerships, fundraising, and grants from Europe and the French Public Investment Bank (BPI),” he said. Most recently, Dracula Technologies was picked in 2022 among 1,000 European startups where it received €1.6 million in grants thanks to the European Innovation Council Accelerator programme.
Its bread and butter is in IoT devices, installed in applications like asset tracking solutions, but also in the smart home, for devices from remote controls to keyboards and digital door locks, recognisable to most, if not all, consumers.
Real-world examples of where Dracula Technologies’ tech has been integrated has involved closely working with semiconductor companies. “Our work with Atmosic resulted in a battery-free remote control powered by their ultra-low-power chip combined with our energy-harvesting module,” Cruchon detailed. “This remote operates entirely on indoor light.”
In another example, “Coolr Group integrated Dracula Technologies’ OPV modules into its VistaZ wire-free cellular camera. By harvesting ambient light, the camera ensures continuous power in cold, low-light environments. It reduces battery replacements, maintenance costs, and downtime while enabling real-time stock monitoring in refrigerators and vending machines.”
Preparing to scale
Cruchon acknowledged the “gradual and complex” growth of the company. “We are now ready to scale production and contribute to the energy sovereignty of France and Europe,” he explained. “Our €8 million investment in an €15 million overall plan revitalises a historic industrial site in Valence, transforming it into a ‘green micropower factory’. ”
The factory in question is based in France and will focus on “frugal innovation principles,” according to Cruchon. Naturally, as a startup that has been conscious of battery waste from the ground up, scaling up production in a factory setting has to be modelled to ensure that resources like electricity and energy aren’t wasted in the endeavour to manufacture its modules.
What does this look like?
“It’s equipped with clean rooms, R&D labs, and automated robots for large-scale OPV production using inkjet printing technology that minimises material consumption,” said Cruchon. “It has the capacity to produce up to 150 million cm² of OPV modules.”
From 2012 to 2025, the gradual and complex growth of the company as Cruchon termed it, has led to industrial scaling of production as the company prepares to not only manufacture OPV modules but support energy independence and bring to market green tech solutions for connected devices that mean in the near future, you won’t have to buy a battery to power your remote control, and you won’t have to throw it away. I’d call that significant progress.
This article originally appeared in the January/February 2025 issue of Startups Magazine. Click here to subscribe