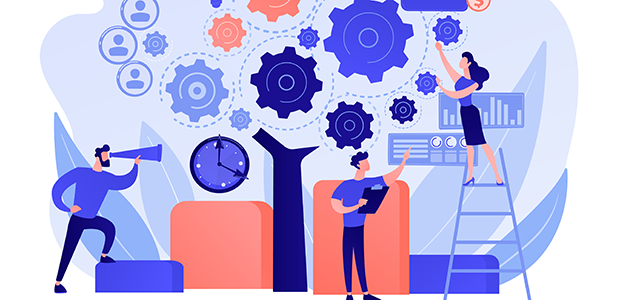
Value stream mapping explained: what is it and how can it boost team productivity?
Operating a competitive business in today’s world is seemingly more complicated than ever. New processes are constantly being developed and integrated, hourly insights and analytics are available for analysis, and even your current method of keeping track of stock is becoming obsolete. But how effective are all these new methods and processes?
If you never stop to reflect on them, you’ll never know.
There are many ways to evaluate your business structure and determine its success or proficiency. Currently, the lean movement is providing one of the more popular models, encouraging businesses of all shapes and sizes to minimise unnecessary wastage to maximise their capability. It seems straightforward enough, but eliminating wasted resources and processing relies on knowing where these are happening.
What is value stream mapping?
Value Stream Mapping (VSM) is all about putting your business process all on one page for everyone to see. It’s particularly helpful at highlighting where production is held up between different processes, as no one is directly responsible for furthering production at that point in the strategy. It gives you the full picture of your company, fitting together the isolated systems at play in siloed departments.
This method of mapping your business can be applied regardless of what commercial product, secure video conferencing software, charity event, or lead generating campaign you produce. If your production goes through multiple processes before the final result, it’s worth setting aside time to create a value stream map. By helping you understand your business better, you can work out where to save time, reduce waste, and increase productivity.
Productivity benefits
There’s nothing worse than your team working their hardest but all their graft is not evident in your key performance indicators, reviews, and end products. Often, this isn’t anything to do with your employees - it’s simply the way a workflow is set up. Value stream mapping can identify areas that are negating your team’s hard work, as well as areas of production that just don’t add value to your product.
Value stream mapping can boost productivity in all sorts of ways, including:
- Pointing out where production slows down with process bottlenecks.
- Highlighting irrelevant processes that either need improving or removing altogether.
- Showing which teams need support to meet the workload and avoid employee stress.
- Helping with overall planning and time-management of projects.
- Identifying the capacity of your business and creating realistic goals for production.
How you use the information from your value stream map can transform your production processes. This doesn’t have to mean finding ways to cut days out of your average production times but could instead translate to improved staffing, more investment in value-adding processes, or having more self-awareness of the abilities and limits of your business.
Create your own value stream map
A value stream map is of no use as an idea in your head. We’ve collected some steps to show you the way forward in creating your map. Every value stream map will look slightly different, as they all focus on different areas and show the processes behind unique and individual businesses. So, the only way to get an idea of what your business processes look like is to make one yourself.
Decide on what you’re mapping
Value stream maps show the processes within your business and how they interlock. However, it’s up to you to decide whether you want to tackle the whole structure at once or create a to do list in excel - from idea to product - or if you want to zoom in on a more specific part of your business. Likewise, you might find you need multiple maps with varying degrees of details. This selection already highlights the number of processes your business does and how they interact with each other.
Identify the stages of production
Work out what happens between the start of production and the end. Everything from content writing and creation to transportation and queuing counts should be mapped out. Look at the processes from the employee perspective, rather than guessing at what goes on from a managerial position. It may surprise you that even at this stage, you may notice key hold-ups in production and where the main problems for your business lie.
Notice the flows
Many value stream maps note particular inter-departmental flows, such as information flows and material flows. These show where knowledge or resources are introduced and how they are passed on to those next in line. You can boost productivity by ensuring all departments use the same communication tools, business software, and methods to transfer these flows onwards. If everyone has access to the same areas, you can reduce the time spent changing the format or checking an item in or out.
Include real-life data
Use the expertise of employees and available metrics to fill your map with data such as current backlog, resources used, and value-added to the product. The more data utilised, the more informative your map becomes. This draws attention to your biggest pulls on time, where order processing software can provide additional help, even which processes to review. These data points are great clues into where to improve your production for maximised productivity.
Find areas of waste
Once you’ve got your value stream map, you can pick up on where your business’s time, energy, and resources are being wasted. You might consider managing built-up backlogs with temporary additional staffing in some departments, minimising overproduction that then requires product storage, or providing your departments with data specific to them, such as analytics for contact centres and key points in the production.
Develop your ideal value stream map
Now you’ve got the hang of creating a value stream map, it can be a useful tool to set productivity goals and design how you want your business processes to look and run in the future. The comparison between your ideal map and the current map can give you a sense of where you are coming from and what tangible steps need to be made to move towards your most productive business.
Boost your team productivity with value stream mapping
Sometimes, we need to take a step back and look at the holistic image of our businesses. Value stream mapping is a great way of doing this, without losing the crucial details of each department’s role and how each process works. Using these maps, you can identify and improve on points of wastage within your company and keep your production line running like a well-oiled machine.