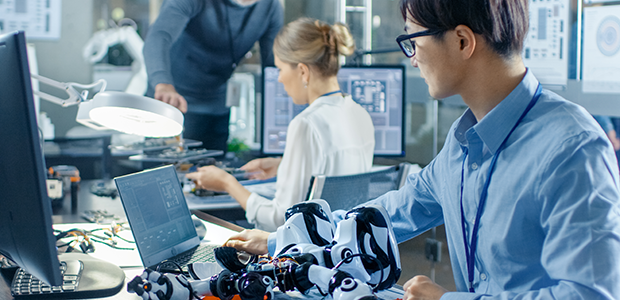
The value of a good prototype and the pitfalls in getting there
This is the second article in Anglia's series taking technology startups through the process of developing a new product. This time it focuses on the second step leading into full production. Your team has been busy developing the hardware and software as well as the aesthetic aspects, the overall look and feel, the user experience. You are now ready to build a prototype before doing final checks and pushing the button to start manufacturing.
Why build a prototype?
But let’s reconnect with the ground for a second. Many young companies going through this product journey for the first time believe that about 80% of the route to market is complete by the time that first prototype is in their hands, and that they will soon be getting paid for their hard work and inspired thinking. In reality, according to Steve Farmer of Pharmatechnics, a design consultant with whom Anglia has worked several times, only about one-third of the hardware journey is complete at this stage.
Steve’s first question, to prospective clients seeking help with their designs, is to ask why they want to build a prototype. The question is not to dissuade, but to focus the project and ensure that the prototype, when built, will provide accurate information for the product to move forward into manufacture. This helps avoid surprises later in the journey that could present any of a number of problems, ranging from delaying the start of production, to impairing manufacturing yield, to usability or reliability issues in the field that can adversely affect market perception. In addition, the prototype can be an essential tool for promoting the start-up. It can be used as part of the process of bringing in investment. Also, it can help secure early engagement from channel partners, so that these are in place when the first production batches appear.
What is a prototype?
The prototype is not the first production model. It is, by definition, some way short of that. However, it needs to resemble the intended finished product in every meaningful way. If it fails in some important respect that impacts upon the end product’s usability, performance, cost, reliability, appearance, or other metrics then it will not have served its purpose, which is to discover these types of problems before production begins. Remedying such issues after committing to production can introduce long delays and is expensive, especially if you have started to make investments in mass production components (which normally need to be bought in bulk before production starts), tooling or specially ordered parts such as an enclosure or custom display.
There is a significant difference in the approach to building a prototype, compared to putting together a proof-of-concept. The two descriptions are often used interchangeably, but the realities are vastly different. The PoC is typically composed of evaluation boards that are simply not of a consistent or suitable quality, and the wiring, connections, and physical arrangement of the various parts simply will not perform in the same way as a properly designed and packaged product.
A prototype must do more than simply validate the design idea and should be close, if not identical, to the final form factor. It provides the first opportunity to touch or hold an object that represents the product closely in terms of its shape, size, finish, weight, balance, and the user interface. It lets you examine integration and fit, the proximity of components to each other to help assess any unexpected interactions between them, the look and feel, and the overall user experience. You can also better visualise and workshop how the product will be assembled and determine any necessary adjustments to processes or materials to improve manufacturability, reduce production costs if possible, and optimise performance in the field.
What else can you learn from the prototype
The prototype also provides the first chance to do some EMC checking and make measurements to assess conformance. There is inevitably some tweaking to do after initial EMC testing, so a good prototype should be representative of the real product’s performance in terms of EMI immunity and as a source of interference signals. Aspects like the distances between components and properties of the case material can all affect the electromagnetic behaviour. Any thermal effects, also, can become evident at this point. You might have a heat source such as a power transistor close to something that’s heat sensitive, or inadequate venting, causing the inside of the product to become a small oven. Steve Farmer comments that this is a common issue. The customer wants clean lines and nice aesthetics, but the hardware needs airflow to remove the heat. Hence the prototype needs to resemble the final product closely, not only electrically but also physically and mechanically.
Of course, the product is about software too and the arrival of the first prototype is the time the software can begin to run on proper hardware. Further development at this stage can be a challenge due to difficult access to certain ports or signals for attaching test gear. There are ways around this, as Steve Farmer points out: ”On one project we designed the production board with small snap-off sections to allow probe access for software development. In production, the snap-offs were removed so that the board could be installed in the enclosure. This gave us a quick and cost-effective way to move from prototype to full production while allowing software development to continue until the last possible moment.”
It can happen that small changes to the design or circuit layout can have a significant impact on the electrical performance. Steve tells of a project update that contained a GPS receiver and an antenna that was changed in favour of a different omnidirectional model and surface-mounted in a new position on the board to better suit the operating needs and new industrial design. The different antenna type, in its changed location, began to pick up a strong signal from a clock trace passing underneath. A harmonic of this clock caused enough interference that the GPS receiver performance was severely degraded. Re-spinning the board to change the clock routing or reposition the GPS antenna would have been expensive. Instead, by studying the issue, the problem was solved in software by changing the operating frequency of the clock. This was a much more cost-effective change than adapting the PCB or repositioning the antenna.
In another project, the prototype showed that the enclosed electronic system was too heavy for the type of enclosure the design team had originally imagined. The problem was the chosen material: a hard and brittle high-gloss polycarbonate that was unable to pass drop testing after the electronics including the circuit board, battery, and display had been installed. Changing to a more resilient hybrid material provided the required strength while allowing an attractive surface finish. The production-accurate prototype highlighted the issue in time for a cost-effective alternative solution to be developed.
Prototype to production
If you are designing a completely new product, you should expect to go through at least two iterations of prototyping before coming up with a production-ready design. More cycles may be necessary, depending on the complexity of the product and the processes being used to build it. On the other hand, if you are updating an already mature product, adding or upgrading features, then one prototype may be enough.
Support at the prototyping stage
There are various ways to access prototyping services, including finding an established independent consultant and using pre-production or new-product introduction (NPI) services frequently offered by contract manufacturers. In addition, a number of our customers have engaged UK-based organisations setup to work directly with Chinese factories that are specialised in making small production runs to a high standard for prototype and research purposes. The production work may then be handed off to another factory, locally to the OEM or offshore.
It's important to remember that taking your first product through development and into a factory is never easy, for anyone. It’s an eye-opener, to say the least, and prototyping is a process that demands intense scrutiny of every aspect of the product – design, performance, compliance, materials, manufacturability, testability – to avoid unwelcome surprises once that commitment to manufacture has been made. You may need to spend thousands, or tens of thousands, of pounds to get through prototyping and into production.
This article originally appeared in the Sept/Oct issue of Startups Magazine. Click here to subscribe.