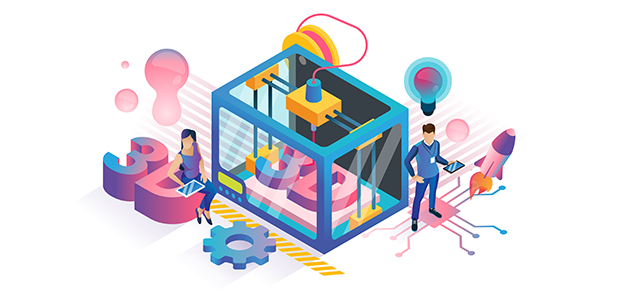
The startups using 3D printing to revolutionise healthcare
From customised prosthetics and implants to detailed anatomical models and even tissue and organ fabrication, the market for 3D printing in healthcare is growing rapidly and startups are playing a huge part.
Advancements in technology, the need for more customisation/personalisation and a surge in R&D investments are key factors driving demand for 3D printing. A shortage of equipment during the COVID-19 pandemic also played a big part.
According to a report published by Allied Market Research, the global 3D printing healthcare market generated $1.03 billion in 2020, and is estimated to reach $5.84 billion by 2030.
Startups are playing a large part in driving forward the growth of the healthcare market and the pandemic has acted as a catalyst, with £38.5bn injected into global healthtech startups in 2021, a 280% increase since 2016.
Here, we look at some recent startups that are using 3D printing to revolutionise this industry:
3D printing helps battle virus spreading
3D printing service provider, MetShape recently supported the research work of startup CIC nanoGUNE – the Basque Nanoscience Cooperative Research Centre. The research involved getting a precise understanding of virus aerosols in order to identify the transmission mechanisms and develop prevention solutions.
The research required virus models to be made that were small, precise and as detailed as possible but conventional 3D printing processes couldn’t offer the precision needed.
MetShape specialises in complex problems and micro-precision parts, so it was able to print a high-precision virus model on the scale 250000:1 with a diameter of approximately 30mm. MetShape said it “was able to print, debind and sinter the model, and provide a finished model to nanoGUNE. No post-processing steps for the virus model were required, as [MetShape's] technology achieves excellent surface quality without the requirement of support structures.”
Prof. Alexander Bittner said, “Thanks to the model printed by MetShape, we can now carry out our experiments on the wetting and dewetting of water on viruses and thus achieve a new milestone in the research of virus aerosols. With the new possibilities through innovative manufacturing technologies, we are taking a big step closer to our long-term goal of protecting as many people as possible from virus infections.”
Putting 3D printing technology directly into the hands of front-line medical professionals
French med-tech startup Bone 3D signed an agreement with Stratasys, a company specialising in 3D printing and additive solutions, materials and services, to deploy 3D printing across France's hospital network.
Via Bone 3D’s Hospifactory initiative, healthcare institutions now have direct access to an immediate, cost-effective and localised way of 3D printing essential medical equipment, medical devices and patient-specific anatomical models.
Healthcare providers can sub-contract 3D printing hardware and services from Bone 3D, granting them the direct means to fulfil their own production needs on-site, as well as receive dedicated ongoing support from Bone 3D technicians.
Jérémy Adam, CEO and Founder, Bone 3D commented: “Early on in the COVID-19 pandemic, the world witnessed the importance of 3D printing first-hand as it provided a swift and direct means of producing vital PPE to equip frontline healthcare workers, ventilator parts and other critical medical equipment.
“However, beyond that, the versatility of 3D printing has seen huge demand from hospitals and medical institutions for a means to create maintenance parts, rehabilitation parts and medical devices. Our Hospifactory initiative will ensure that some of the market’s most advanced 3D printing technologies are made accessible exactly where and when they are needed by surgeons and clinicians across the French hospital network.”
Last year, Bone 3D deployed 60 Stratasys FDM 3D printers in Europe’s largest hospital system, the AP-HP in Paris, to support the frontline fight against COVID-19. Bone 3D managed the implementation, operation and support of the fleet, which gave the AP-HP its own in-house capability to produce vital PPE, electrical syringe pumps, intubation equipment and respirator valves on-demand, bridging the shortfall in traditionally manufactured equipment.
Developing 3D biofabricated tissues to treat kidney failure
Organ Donation Statistics reveal that 17 people die every day waiting for an organ transplant and there are currently 106,228 people on the waiting list. Advances in 3D printing have assisted in the building of living tissue constructed into the shape of human organs. However, 3D printed human tissues lack the cellular density and organ-level functions required for them to be used in organ repair or replacement.
In light of this, researchers from Harvard’s Wyss Institute for Biologically Inspired Engineering and John A. Paulson School of Engineering and Applied Sciences (SEAS) created a technique called SWIFT (sacrificial writing into functional tissue). Co-first author Mark Skylar-Scott, Ph.D., a Research Associate at the Wyss Institute explains the process: “Rather than trying to 3D print an entire organ’s worth of cells, SWIFT focuses on only printing the vessels necessary to support a living tissue construct that contains large quantities of organ building blocks (OBBs), which may ultimately be used therapeutically to repair and replace human organs with lab-grown versions containing patients’ own cells.”
Now, Trestle Biotherapeutics, a newly launched startup, aims to translate this technology to address the growing need for kidney tissues and organs. The startup has been granted a license by Harvard University to commercialise a suite of stem-cell and 3D bioprinting-based kidney regenerative medicine technologies. The combination of stem-cell and 3D bioprinting engineering could enable new approaches to treating kidney diseases.
“We’re very excited to bring the biofabrication and stem cell biology technologies developed in the Lewis and Morizane labs into what we are building at Trestle. The teams at Harvard, Wyss, and the Brigham have a renowned track record in translational innovation, and we’re thrilled with the opportunity to carry their work forward for patients’ benefit,” said Ben Shepherd, the CEO of Trestle.