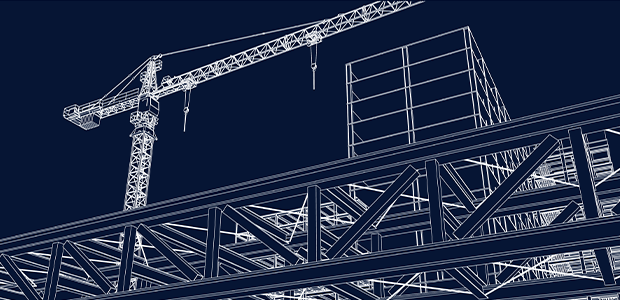
Digitalisation: Transforming the UK Construction Industry with Technology
"By adopting advanced technologies like BIM, project management software, and digital marketplaces for buying and selling timber, the industry can improve efficiency, cut costs, and enhance project outcomes," writes David de Jong, CEO of VonWood.
The UK construction sector has been plagued by significant challenges in the past few years, particularly in terms of delays, material and labour shortages. For example, brick deliveries decreased by 4.3% in April 2024 compared with April 2023 and have been following a steady decline since 2022. Block deliveries are declining even further, falling by 9.8% in April 2024 compared to April 2023. The picture looks very similar when it comes to labour availability. According to Coleman Group, the UK needs to hire around 266,000 extra construction workers by 2026, the equivalent of 53,200 a year, to meet the current construction output.
Factors like these, as well as others like inflation, have resulted in building costs increasing sharply. As such, it’s crucial to continuously search for ways to improve our building methods. Digitalisation offers one such solution.
How digitalisation is revolutionising construction
The advent of digitalisation is reshaping the construction industry by streamlining processes and enhancing project efficiency. One of the most impactful advancements is Building Information Modelling (BIM). BIM allows the creation of comprehensive 3D models that include every aspect of a building, from its structural components to its electrical systems. This technology facilitates superior planning and coordination among all stakeholders, significantly reducing errors and delays.
Another digitally enabled innovation is off-site manufacturing, also known as prefabrication or modular construction. This method involves producing building components in a controlled factory environment before assembling them on-site. Prefabrication can cut project timelines by up to 50% compared to traditional methods, leading to cost savings due to reduced labour and on-site time.
Before these production benefits can even be realised, digitalisation is able to streamline the entire supply and procurement process, from harvesting timber to delivering it to factories. While some parts of the supply chain have integrated digital technologies, the timber trade remains largely traditional in many areas, leading to still many transactions being done based on who you know and not what is most effective. However, new platforms and marketplaces are transforming how timber is bought and sold.
Enhancing cost efficiency in construction
Digitalisation significantly impacts construction costs by boosting efficiency and reducing waste. Advanced project management software enhances resource allocation and scheduling, minimising downtime and optimising labour, thus lowering costs. Digital supply chain management systems provide real-time tracking of materials, enabling better planning for deliveries and reducing the risk of shortages. And with new legislations around the corner (EUDR), having full access to raw material source information is crucial.
The role of timber during scarcity
Different construction materials typically do not face shortages simultaneously unless global events, like the Suez Canal blockage or the Covid-19 pandemic, disrupt supply chains. Timber, usually in stable supply, can substitute for materials like concrete or steel when they become scarce or costly. However, during periods of sharply increased demand, such as the Covid-19 home renovation boom, timber supplies can struggle to keep pace since trees need time to grow. Therefore, timber alone cannot fully resolve shortage issues. Nevertheless, dedicated planting and harvesting for timber ensures a stable, sustainable supply in the long run.
Timber also offers significant environmental benefits. Each cubic metre of timber used in construction sequesters approximately 0.9 tonnes of CO2e, storing it for the building's lifetime. This feature supports global carbon reduction efforts and promotes sustainability in construction, making timber a more environmentally friendly option compared to traditional materials.
Where is it leading to?
Digitalisation provides transformative solutions to the construction industry's challenges of delays and material shortages. By adopting advanced technologies like BIM, project management software, and digital marketplaces for buying and selling timber, the industry can improve efficiency, cut costs, and enhance project outcomes. Prefabrication, particularly using timber, offers a sustainable and efficient alternative to traditional construction methods, addressing both material shortages and environmental concerns. As the UK construction industry continues to embrace digitalisation, it can anticipate a future marked by more efficient, sustainable, and cost-effective building practices.